Formnext 2016│華曙高科3D打印助您破解傳統汽車生產四大痛點
時間:2016-11-04 15:53 來源:中國3D打印網 作者:中國3D打印網 閱讀:次
幾百人的研發團隊、4至5年、近5至10億人民幣……沒錯,這就是開發一個全新整車產品需要消耗的巨大資源。目前,我國的汽車零部件行業生產工藝、制造水準還不能滿足整車廠大部分的要求,核心技術幾乎均被跨國公司壟斷,實現技術創新似乎還很遙遠。
汽車市場競爭日益激烈,需求瞬息萬變,形勢嚴峻顯而易見,各大汽車制造企業都意識到研發速度、成本控制及技術能力在未來將愈加重要。而傳統汽車制造業的四大痛點,你踩中了幾個?
痛點一:整車研發周期長達5年
整車開發周期對產品投放市場的時機有著決定性的影響,但從產品規劃直至投放市場,是一個冗長復雜的過程。整車研發流程最長需要經歷57個月,主要包括部件研發及集成、系統驗證及汽車制造和質量控制。制造工作中最耗時的工作就是工裝設備的制造以及模具的開發,時間前后加起來要接近一年。
3D打印:研發周期縮短53%
華曙高科3D打印技術優勢在于能快速更改設計差錯、提高生產效率、降低開發成本。相較于傳統的模具開發,以及鍛造、鑄造等復雜的工藝,簡化了中間環節,縮短開發周期。相對于目前國內零部件15天以上的開發周期,3D打印技術依據零部件的復雜程度,只需要1~7天的開發周期。
痛點二:創新研發受限
3D打印:復雜結構一體成型
華曙高科3D打印技術以逐層累加的方式完成加工,將制件的三維復雜的不規則曲面、鏤空異形結構,轉化為簡單的平面結構進行成型,突破了傳統加工技術的壁壘,尤其在具有復雜內部結構及嵌套的制件上,可一次成型,相比之下更加具有優勢。
痛點三:輕量化不足
輕量化意味著一輛汽車擁有更好的操作性、更快的加速度、更短的剎車距離、更少的油耗及更優異的環保性能,將大大提升汽車的市場競爭力。目前構成汽車的2萬多個零件中,約86%是金屬材料,且鋼鐵占了約80%,這表明通過材料的輕量化來減輕汽車自重有巨大潛力。同時,在汽車很多關鍵的位置,常常需要兩種甚至兩種以上的材料進行拼焊,有些還要加注結構膠,以實現隔音、提高密封性或增加連接強度等目的,這在無形中也增加了汽車的整體重量。
▲ 華曙高科運用PA6材料3D打印的汽車進氣總管
3D打印:運用新材料提升輕量化
3D打印技術在汽車輕量化產品中開發中占據了越來越重要的位置,因為此技術可以使得塑料乃至金屬制造中空的輕量化結構零件成為了可能,而不單單依靠發泡和微發泡技術。另外,華曙高科聯合巴斯夫、LSS成功研發PA6材料,采用這種創新材料生產的物品具有更出色的強度和熱穩定性,更適合航天航空、汽車行業應用領域,且具有良好的可回收性,能大大提升汽車輕量化性能。
痛點四:生產成本高
導致汽車制造企業生產成本居高不下的原因主要有零部件開模費用昂貴、材料利用率低及人力成本高等因素。選擇合適的沖壓工藝、不斷優化模具結構、充分考慮材料利用率和提升技術創新力等,直接決定著汽車制造成本,對整車成本控制具有十分重要的意義。
▲ 華曙高科運用PA6材料3D打印的汽車后視鏡
3D打印:研發成本下降54%
以空調總成系統為例,通過傳統工藝進行結構設計,需要多次開模,開模的成本一次可能需要5萬左右,而單次使用3D打印生產的成本費用僅為2.5萬左右,研發成本下降54%,大大提高了市場競爭力。音符汽車行業競爭激烈,技術改革迫在眉睫! 2016年11月15日至18日,華曙高科將攜手全球戰略合作伙伴巴斯夫、LSS及Lehmann&Voss聯合參展德國法蘭克福Formnext展會,現場發布并展示華曙高科最新3D打印應用解決方案,以及在激光燒結設備、材料、技術和服務等方面的合作。
該方案不僅能為客戶提供更好的質量,更具吸引力低的價格,還能滿足汽車等行業對于擁有大尺寸、輕重量、耐高溫零部件的需求,將重新定義未來汽車零部件的制造方式。

痛點一:整車研發周期長達5年
整車開發周期對產品投放市場的時機有著決定性的影響,但從產品規劃直至投放市場,是一個冗長復雜的過程。整車研發流程最長需要經歷57個月,主要包括部件研發及集成、系統驗證及汽車制造和質量控制。制造工作中最耗時的工作就是工裝設備的制造以及模具的開發,時間前后加起來要接近一年。
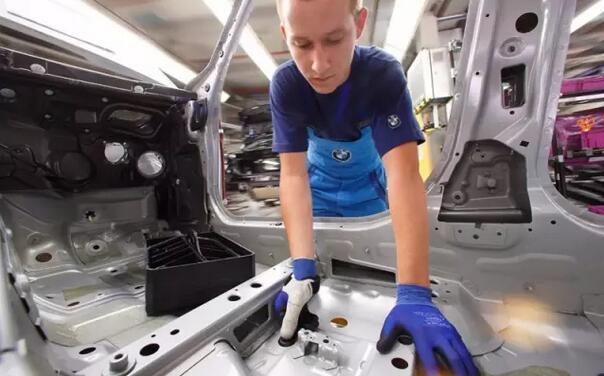
3D打印:研發周期縮短53%
華曙高科3D打印技術優勢在于能快速更改設計差錯、提高生產效率、降低開發成本。相較于傳統的模具開發,以及鍛造、鑄造等復雜的工藝,簡化了中間環節,縮短開發周期。相對于目前國內零部件15天以上的開發周期,3D打印技術依據零部件的復雜程度,只需要1~7天的開發周期。
痛點二:創新研發受限
傳統的汽車制造工藝往往需要特殊的沖壓模具,費時費力,設計方面受到工藝影響具有諸多限制,陷入創新思維向工藝妥協的怪圈。比如在汽車集線插板制造過程中,其內部有很多凹槽、卡扣類結構,手辦件難以開模制作,且費用昂貴。
3D打印:復雜結構一體成型
華曙高科3D打印技術以逐層累加的方式完成加工,將制件的三維復雜的不規則曲面、鏤空異形結構,轉化為簡單的平面結構進行成型,突破了傳統加工技術的壁壘,尤其在具有復雜內部結構及嵌套的制件上,可一次成型,相比之下更加具有優勢。
痛點三:輕量化不足
輕量化意味著一輛汽車擁有更好的操作性、更快的加速度、更短的剎車距離、更少的油耗及更優異的環保性能,將大大提升汽車的市場競爭力。目前構成汽車的2萬多個零件中,約86%是金屬材料,且鋼鐵占了約80%,這表明通過材料的輕量化來減輕汽車自重有巨大潛力。同時,在汽車很多關鍵的位置,常常需要兩種甚至兩種以上的材料進行拼焊,有些還要加注結構膠,以實現隔音、提高密封性或增加連接強度等目的,這在無形中也增加了汽車的整體重量。
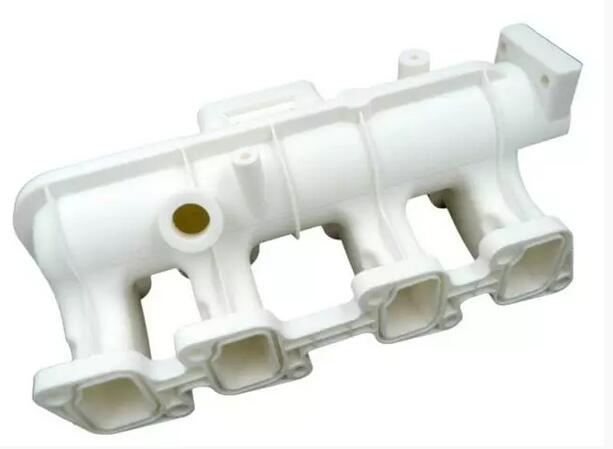
▲ 華曙高科運用PA6材料3D打印的汽車進氣總管
3D打印:運用新材料提升輕量化
3D打印技術在汽車輕量化產品中開發中占據了越來越重要的位置,因為此技術可以使得塑料乃至金屬制造中空的輕量化結構零件成為了可能,而不單單依靠發泡和微發泡技術。另外,華曙高科聯合巴斯夫、LSS成功研發PA6材料,采用這種創新材料生產的物品具有更出色的強度和熱穩定性,更適合航天航空、汽車行業應用領域,且具有良好的可回收性,能大大提升汽車輕量化性能。
痛點四:生產成本高
導致汽車制造企業生產成本居高不下的原因主要有零部件開模費用昂貴、材料利用率低及人力成本高等因素。選擇合適的沖壓工藝、不斷優化模具結構、充分考慮材料利用率和提升技術創新力等,直接決定著汽車制造成本,對整車成本控制具有十分重要的意義。
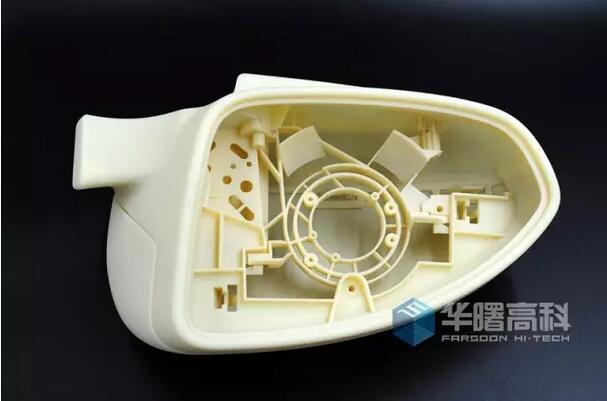
▲ 華曙高科運用PA6材料3D打印的汽車后視鏡
3D打印:研發成本下降54%
以空調總成系統為例,通過傳統工藝進行結構設計,需要多次開模,開模的成本一次可能需要5萬左右,而單次使用3D打印生產的成本費用僅為2.5萬左右,研發成本下降54%,大大提高了市場競爭力。音符汽車行業競爭激烈,技術改革迫在眉睫! 2016年11月15日至18日,華曙高科將攜手全球戰略合作伙伴巴斯夫、LSS及Lehmann&Voss聯合參展德國法蘭克福Formnext展會,現場發布并展示華曙高科最新3D打印應用解決方案,以及在激光燒結設備、材料、技術和服務等方面的合作。
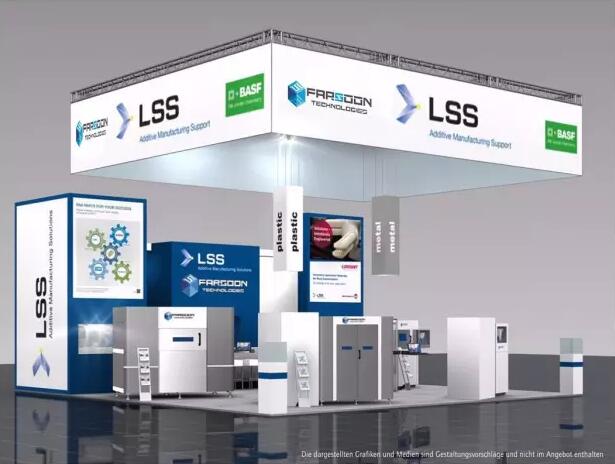
該方案不僅能為客戶提供更好的質量,更具吸引力低的價格,還能滿足汽車等行業對于擁有大尺寸、輕重量、耐高溫零部件的需求,將重新定義未來汽車零部件的制造方式。
(責任編輯:admin)
最新內容
熱點內容