金屬粉芯焊絲電弧增材制造的顯微組織與力學性能
時間:2024-01-16 09:27 來源:增材制造碩博聯盟 作者:admin 閱讀:次
電弧增材制造(WAAM)是一種基于弧焊工藝的3D金屬打印技術。WAAM采用傳統焊絲作為線材,沉積速率高且成本低,因而適合于生產大型金屬部件。需要指出的是,在一些鋼部件生產中,需要根據鋼種需求生產單一部件,若采用商用焊絲無法滿足。本研究通過WAAM對由金屬粉芯制成的中碳鋼(Grade
XC-45,與XC-45鍛造材料成分相似)進行了薄壁沉積。之所以選擇這種特殊成分,是因為它對按需生產重載航空部件意義重大。本研究對沉積部件的微觀結構、硬度以及抗拉強度進行了研究,并對試樣進行了金相研究。由于建造過程涉及多次熱循環,因此在微觀結構上,可發現明顯局部變化。盡管如此,從頂部到底部,該部件硬度相對均勻。水平方向(沉積方向)平均曲度/抗拉強度為620
MPa/817 MPa,垂直方向(構建方向)為580 MPa/615
MPa。兩方向延伸率差異顯著,水平方向為6.4%,垂直方向為11%。最后,根據從金相研究中觀察到的凹陷結構,本研究確定了延性破裂模式。此外,本研究還針對機械性能,將WAAM與鑄造、熔鑄及冷軋工藝等進行了一個比較。結果表明,采用研究專門設計的金屬粉芯,能生產出硬度分布更均勻及抗拉強度更高的合金。
1. 引言
增材制造(AM)通過專用的3D CAD模型,逐層沉積材料,直接生產3D組件。對于幾何形狀及成分較復雜的組件,采用傳統鍛造工藝難以實現,而AM 在這一方面則有一定優勢。電弧增材(WAAM)是一種以電弧為熱源及熔嘴為線材的增材制造技術,可以視其為對傳統GMAW工藝的改進。由于其沉積速率高,與基于粉末的直接能量沉積(DED)技術相比,WAAM下材料利用率高,交工時間短,因此WAAM技術已被應用于航空、汽車和海洋領域。此外,金屬氣體弧焊(GMAW)、鎢極氣體弧焊(GTAW)和等離子弧焊(PAW)等幾種傳統的電弧焊技術也已被應用在了WAAM上,由于它們的沉積特征不同,因此應用領域也就有所差異。此外,人們還發明了冷金屬過渡(CMT)和冷連軋GMAW等GMAW衍生工藝,用于提高以為GMAW為基礎的WAAM工藝的沉積質量和效率。然而,從現有的這些工藝來看,由于沉積速率更快(可達160 g/min),GMAW成為短時間內生產大型零件的理想工藝,以及WAAM中最受歡迎的工藝。將WAAM運用于海洋領域大型部件制造的一個例子是WAAMpeller,它是世界上第一個獲批的3D打印船舶螺旋槳。
據作者所知,WAAM工藝應用并未覆蓋至現今所有焊材,只有少數機構致力于開發WAAM工藝下合金。由于目前只有少量生產需要運用WAAM工藝,因此對特殊合金的市場需求并不具備商業吸引力。只有當涉及大部件生產時,涉及特定化學成分鑄造和拉制的實心焊絲工藝才具有經濟可行性。目前WAAM工藝應用正在逐步增長,其將促進WAAM耗材的發展。WAAM應用通常指的是小批量生產或原型制造,它們通常需要特殊的線材組合,或者通過特定耗材組合以獲得理想部件。金屬芯焊絲特別適用于生產一次性或小批量的消耗性成分。金屬芯焊絲由金屬護套和填充了各種粉末的芯線組成。同藥芯焊絲相比,金屬芯中助焊劑數量減少,這有利于控制焊縫金屬中雜質的形成。此外,金屬芯焊絲的合金成分可以得到進一步優化,以降低某些焊接缺陷生成率,如裂紋和氣孔。金屬芯焊絲還適用于修復或制造化學成分與現有焊接消耗品不匹配的部件。由于金屬芯具有以上靈活性,因此其運用可以為WAAM帶來顯著好處。
金屬芯線由實心護套和粉末芯線組成(如圖1),其硬度不如實心芯線。在沉積過程中,金屬芯導線只通過護套傳導電流,從而產生更高的電流密度。所述護套內的粉末被電弧熔化,從而形成朝向所述基座的粉末噴槍。然而,粉末噴槍中并沒有發生能量轉移,因此熔化相同體積的金屬芯導線所需能量要小于實心導線。在這種情況下,WAAM部件熱輸入減少,有利于降低穿透。此外,為了獲得類似的沉積特性,如珠形、縱橫比和沉積速度等,金屬芯焊絲所需電流相對較低,這有利于WAAM工藝。
在過去的二十年中,上述金屬芯焊絲的優點引起了眾多研究者和研究機構的關注。研究表明,金屬芯焊絲適用于增材制造。然而,到目前為止,只有少量金屬芯焊絲在WAAM中得到應用并形成了相關研究。關注公眾號: 增材制造碩博聯盟,免費獲取海量增材資料,聚焦增材制造科研與工程應用!
本文研究了一種基于GWAM工藝的金屬芯焊絲。之所以選擇這種特殊成分,一方面是因為它對重載航空航天部件生產具有特別的意義,另一方面是因為這種化學成分在商用焊絲中并不存在。本研究對沉積單珠壁的外觀、微觀結構、曲度/拉伸強度及金相組織進行了研究,為WAAM的潛在應用提供了相應依據。
2. 材料及方法
本研究使用的S355結構鋼底板為250 × 60 × 10 mm3。填充材料為XC-45(標準AFNOR, NF A37-502)金屬芯絲,直徑為1.2 mm。本研究所用材料化學成分見表1。XC-45化學成分為沉積金屬成分,由直讀光譜儀測量所得。在沉積之前,用丙酮((CH3)2CO)溶液清洗基面。
沉積使用松下機械臂(圖2a)和由Valk焊接集成的電源進行。采用Autodesk PowerMill為設計沉積工具路徑的軟件。本研究實驗設置如圖2b所示,包括沉積方向、構建方向和夾具位置。焊炬位置垂直于工件(PA位置)。采用如圖2c所示的沉積策略,即反轉每層的沉積方向,以避免啟動區和停止區之間產生高度差。通過提高送絲速度(4-8 m/min),以良好的珠粒外觀和合適的寬高比為基礎,選擇最佳沉積條件。本研究使用的參考沉積參數如表2所示。
實驗共沉積90層,每層由一個珠粒組成。每層沉積后,對壁面進行風冷,直到頂面溫度測量達到室溫,與此同時,保持接觸尖端到工作距離(CTWD)高1mm。
為進行冶金和力學研究,實驗制備了沉積壁樣品。制備截面采用2% Nital(98%乙醇和2% HNO3)刻蝕,用于光學顯微鏡觀察(Keyence VHX-5000)。根據DIN EN 6892-1標準,采用Instron-5550拉伸試驗機在室溫下進行測試;根據ASTM E8M-09標準,在垂直方向和水平方向制備拉伸試樣,如圖3所示。此外,使用JEOL JSM-IT100掃描電子顯微鏡(SEM)進行了斷口金相研究。相分析采用能量色散光譜(EDS)。利用JEOL FEG-SEM JSM 5600F掃描電子顯微鏡(SEM)進行了高分辨率微觀結構特征觀察。在壁橫截面上測量維氏硬度(HV2,2 kgf),方向為從頂部到底部,使用Struers durascan70機器。縮進路徑為如圖4a所示。
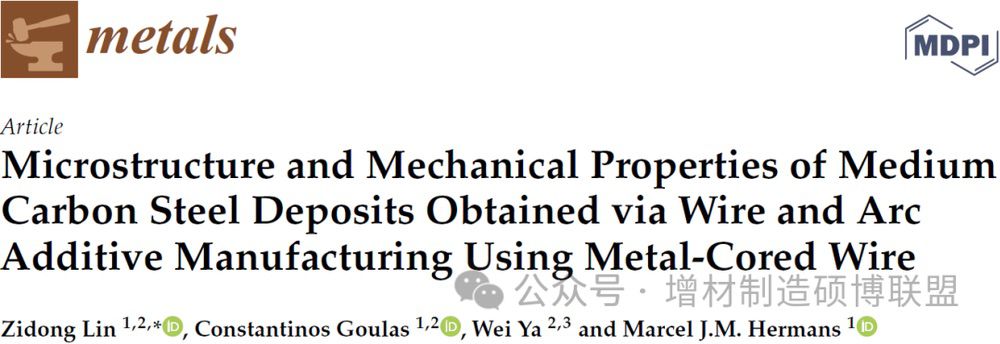
1. 引言
增材制造(AM)通過專用的3D CAD模型,逐層沉積材料,直接生產3D組件。對于幾何形狀及成分較復雜的組件,采用傳統鍛造工藝難以實現,而AM 在這一方面則有一定優勢。電弧增材(WAAM)是一種以電弧為熱源及熔嘴為線材的增材制造技術,可以視其為對傳統GMAW工藝的改進。由于其沉積速率高,與基于粉末的直接能量沉積(DED)技術相比,WAAM下材料利用率高,交工時間短,因此WAAM技術已被應用于航空、汽車和海洋領域。此外,金屬氣體弧焊(GMAW)、鎢極氣體弧焊(GTAW)和等離子弧焊(PAW)等幾種傳統的電弧焊技術也已被應用在了WAAM上,由于它們的沉積特征不同,因此應用領域也就有所差異。此外,人們還發明了冷金屬過渡(CMT)和冷連軋GMAW等GMAW衍生工藝,用于提高以為GMAW為基礎的WAAM工藝的沉積質量和效率。然而,從現有的這些工藝來看,由于沉積速率更快(可達160 g/min),GMAW成為短時間內生產大型零件的理想工藝,以及WAAM中最受歡迎的工藝。將WAAM運用于海洋領域大型部件制造的一個例子是WAAMpeller,它是世界上第一個獲批的3D打印船舶螺旋槳。
據作者所知,WAAM工藝應用并未覆蓋至現今所有焊材,只有少數機構致力于開發WAAM工藝下合金。由于目前只有少量生產需要運用WAAM工藝,因此對特殊合金的市場需求并不具備商業吸引力。只有當涉及大部件生產時,涉及特定化學成分鑄造和拉制的實心焊絲工藝才具有經濟可行性。目前WAAM工藝應用正在逐步增長,其將促進WAAM耗材的發展。WAAM應用通常指的是小批量生產或原型制造,它們通常需要特殊的線材組合,或者通過特定耗材組合以獲得理想部件。金屬芯焊絲特別適用于生產一次性或小批量的消耗性成分。金屬芯焊絲由金屬護套和填充了各種粉末的芯線組成。同藥芯焊絲相比,金屬芯中助焊劑數量減少,這有利于控制焊縫金屬中雜質的形成。此外,金屬芯焊絲的合金成分可以得到進一步優化,以降低某些焊接缺陷生成率,如裂紋和氣孔。金屬芯焊絲還適用于修復或制造化學成分與現有焊接消耗品不匹配的部件。由于金屬芯具有以上靈活性,因此其運用可以為WAAM帶來顯著好處。
金屬芯線由實心護套和粉末芯線組成(如圖1),其硬度不如實心芯線。在沉積過程中,金屬芯導線只通過護套傳導電流,從而產生更高的電流密度。所述護套內的粉末被電弧熔化,從而形成朝向所述基座的粉末噴槍。然而,粉末噴槍中并沒有發生能量轉移,因此熔化相同體積的金屬芯導線所需能量要小于實心導線。在這種情況下,WAAM部件熱輸入減少,有利于降低穿透。此外,為了獲得類似的沉積特性,如珠形、縱橫比和沉積速度等,金屬芯焊絲所需電流相對較低,這有利于WAAM工藝。

圖1 比較了金屬芯焊絲與實心焊絲的截面以及在短路轉換模式下兩者的金屬能量轉移模式
在過去的二十年中,上述金屬芯焊絲的優點引起了眾多研究者和研究機構的關注。研究表明,金屬芯焊絲適用于增材制造。然而,到目前為止,只有少量金屬芯焊絲在WAAM中得到應用并形成了相關研究。關注公眾號: 增材制造碩博聯盟,免費獲取海量增材資料,聚焦增材制造科研與工程應用!
本文研究了一種基于GWAM工藝的金屬芯焊絲。之所以選擇這種特殊成分,一方面是因為它對重載航空航天部件生產具有特別的意義,另一方面是因為這種化學成分在商用焊絲中并不存在。本研究對沉積單珠壁的外觀、微觀結構、曲度/拉伸強度及金相組織進行了研究,為WAAM的潛在應用提供了相應依據。
2. 材料及方法
本研究使用的S355結構鋼底板為250 × 60 × 10 mm3。填充材料為XC-45(標準AFNOR, NF A37-502)金屬芯絲,直徑為1.2 mm。本研究所用材料化學成分見表1。XC-45化學成分為沉積金屬成分,由直讀光譜儀測量所得。在沉積之前,用丙酮((CH3)2CO)溶液清洗基面。

表1 底板及焊絲化學成分
沉積使用松下機械臂(圖2a)和由Valk焊接集成的電源進行。采用Autodesk PowerMill為設計沉積工具路徑的軟件。本研究實驗設置如圖2b所示,包括沉積方向、構建方向和夾具位置。焊炬位置垂直于工件(PA位置)。采用如圖2c所示的沉積策略,即反轉每層的沉積方向,以避免啟動區和停止區之間產生高度差。通過提高送絲速度(4-8 m/min),以良好的珠粒外觀和合適的寬高比為基礎,選擇最佳沉積條件。本研究使用的參考沉積參數如表2所示。
實驗共沉積90層,每層由一個珠粒組成。每層沉積后,對壁面進行風冷,直到頂面溫度測量達到室溫,與此同時,保持接觸尖端到工作距離(CTWD)高1mm。
為進行冶金和力學研究,實驗制備了沉積壁樣品。制備截面采用2% Nital(98%乙醇和2% HNO3)刻蝕,用于光學顯微鏡觀察(Keyence VHX-5000)。根據DIN EN 6892-1標準,采用Instron-5550拉伸試驗機在室溫下進行測試;根據ASTM E8M-09標準,在垂直方向和水平方向制備拉伸試樣,如圖3所示。此外,使用JEOL JSM-IT100掃描電子顯微鏡(SEM)進行了斷口金相研究。相分析采用能量色散光譜(EDS)。利用JEOL FEG-SEM JSM 5600F掃描電子顯微鏡(SEM)進行了高分辨率微觀結構特征觀察。在壁橫截面上測量維氏硬度(HV2,2 kgf),方向為從頂部到底部,使用Struers durascan70機器。縮進路徑為如圖4a所示。
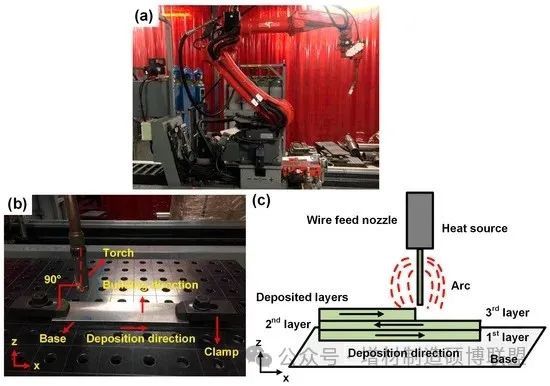
圖2 (a)機器人導線及電弧增材(WAAM)設置,(b)實驗設置,(c)本研究沉積工具路徑
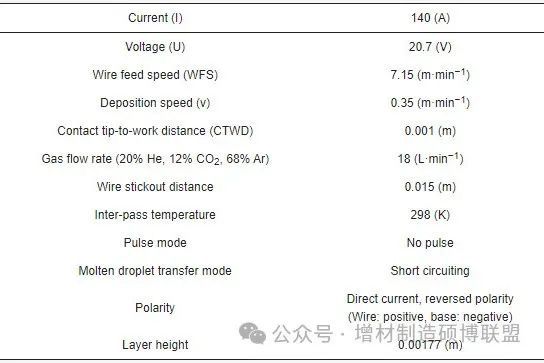
表2 研究中使用到的參考沉積基數
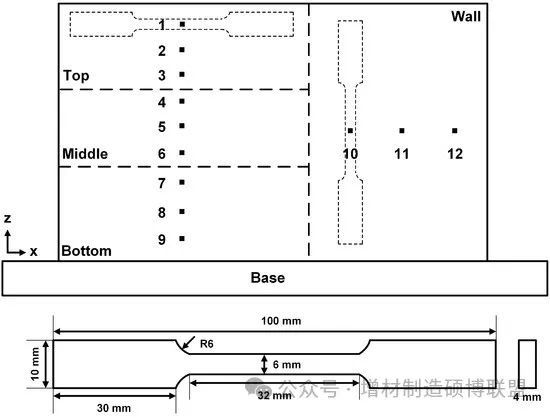
圖3 從樣本中提取到的拉伸試樣示意圖
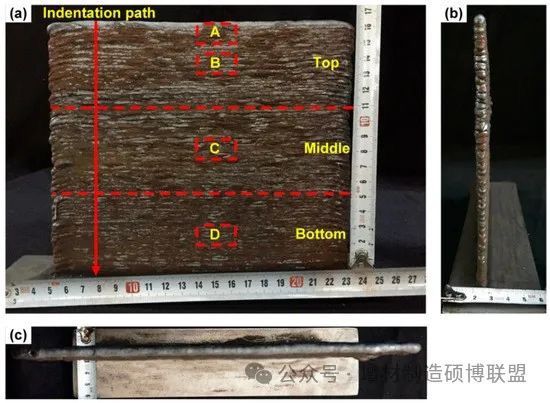
圖4 采用XC-45鋼絲并經WAAM沉積的單珠壁,(a)主視圖,(b)側視圖,(c)俯視圖 (根據表2列出的沉積參數)
(責任編輯:admin)
最新內容
熱點內容