粉末基增材制造金屬和合金過程的多尺度缺陷的形成原因及修正方法
時間:2024-01-16 09:30 來源:航空燃機資訊 作者:admin 閱讀:次
由于增材制造(AM)技術提供了出色的設計自由度,具有復雜幾何形狀的部件可以基于預定義的計算機輔助設計(CAD)模型輕松地逐層制造。各種 AM 技術已經被開發并廣泛應用于設計和制造用于關鍵工業應用的高性能組件,包括航空航天,醫療和汽車領域。
基于粉末的增材制造金屬和合金中多尺度缺陷的類型包括尺寸缺陷、表面質量缺陷、顯微組織缺陷以及成分缺陷。香港理工大學、西北工業大學和香港中文大學的傅銘旺教授等人提出了基于粉末的增材制造金屬和合金過程中的多尺度缺陷,并闡明了各類缺陷形成的潛在機制以及控制方法;總結了金屬增材制造各類缺陷的破壞性和非破壞性檢測方法;介紹了多尺度增材制造缺陷建模的研究進展;分析討論了各類缺陷對增材制造件的拉伸及疲勞力學性能的影響機制。
多尺度缺陷的分類概覽
金屬 AM 部件的性能在很大程度上取 決于其表面質量和微觀結構特征。影響表面質量和微結構的主要因素包括材料性能、設計相關因素、工藝參數和系統設置。不適當的工藝配置可能會在最終的 AMed 組件中引入缺陷,例如孔隙和裂紋。基于現有的金屬 AM 文獻,在 AMed 金屬零件和結構中識別出從毫米到納米尺度的多尺度缺陷。如圖所示,將多尺度缺陷主要分為三大類,即幾何相關缺陷、表面完整性相關缺陷和微結構缺陷。特別地,我們首先將織構柱狀晶粒,復合-結構缺陷和位錯細胞在 AMed 件中普遍存在,并對 AMed 元件的性能產生重要影響。
1幾何相關缺陷
幾何缺陷主要來自于制造結構與理想 CAD 模型之間 的尺寸和幾何偏差。幾何相關缺陷主要包括零件變形和分層。分層是AM 過程中獨特的開裂行為,這是由于 AM 的逐層制造模式的性質所決定的。典型的零件變形和分層如圖 (a-c)]所示。零件變形和脫層是由宏觀殘余應力引起的,而宏觀殘余應力來源于空間熱 梯度
例如,零件在熱循環過程中的不均勻膨脹和收縮,以及不均勻的非彈性應變。影響殘余應力相關變形的因素有很多。與設備相關的因素包括激光光斑尺寸、基板的厚度和預熱等,都可能誘發這類缺陷。在我們寶貴的工作中,我們比較了微 LPBF(使用直徑為 25 m 的細激光束)和常規 LPBF 產生的懸臂梁的畸變。如圖 (a.d)所示,由于原位應力消除退火更顯著,精細激光束產生的畸變更小。因此,微型 LPBF 系統更有可能生產出幾何精度高的部件。此外,Corbin 等研究了襯底厚度和預熱對 DED Ti6A14V 變形的影響。他們得出結論:襯底預熱后,薄襯底的畸變有效降低,而厚襯底的畸變則增加。因此,選擇合適的基板厚度和預熱溫度來減少殘余應力是很重要的。
研究了激光功率、掃描速度、掃描層厚度和掃描策略等工藝參數對殘余應力和零件變形的影響。Mugwagwa
等人報道了掃描速度和激光功率的增加導致由殘余應力引起的 LPBFed
懸壁變形總體呈增加趨勢,增加層厚會減少變形,但由于能量密度降低而增加孔隙率。Salem
等利用橋曲率法探討了掃描策略對畸變的影響,結果表明,通過縮短掃描矢量,畸變幅度減小。相應地,Promoppatum 和 Yao報道,在
Ti6A14V的 SLM 中分別使用 5 mm 和 1 mm 的掃描長度時,殘余應力從 185 MPa 降低到 90 MPa(圖
(e))。工藝參數對殘余應力影響的類似趨勢也在中進行了回顧。
零件變形的設計相關因素包 括零件在基材上的方向和位置、零件形狀、特征尺寸直接金屬激光燒結 Ti6A14V 零件的幾何精度。結果表明,幾何誤差隨著特征尺寸的增加而減小并收斂到一個恒定值,表明尺寸相關收縮是幾何不精度的原因。此外,懸空或突出特征在復雜結構中很常見,但由于缺乏底部支撐,它們難以通過 AM對于 PBF 工藝,粉末床可以作為這些結構的支撐。然而,由于粉末床與固體懸垂結構之間的電導率差異,可能會產生集中的殘余應力,導致結構翹曲、卷曲和變形。因此,當構件具有懸垂或突出特征時,需要設計支撐結構。除了支撐懸垂特征外,良好的支撐結構設計還可以保證正確的熱流流向基材,防止因高殘余應力而產生較大的變形。
2表面完整性相關缺陷
表面完整性缺陷是指與 CAD 設計模型的理想輪廓相偏離的不均勻或不規則的表面特征。我們總結了造成 AMed 部件表面完整性相關缺陷的四個主要因素,即階梯效應、部分熔化的粉末、球化效應和表面裂紋。與機械加工等傳統制造工藝相比,這些缺陷導致表面粗糙度較高,質量和精度較低,這是 AM 工藝固有的局限性之一.
階梯效應是指由于制造分辨率的限制,曲面和斜面的層層逐級通近。樓梯效應引起的平均表面粗糙度(Ra)由層厚度和相對于建筑方向的傾斜角(BD)決定。增加層厚會導致顯著的樓梯效應和更大的表面粗糙度。對于 AM 的晶格結構,這種帶有懸挑支柱的復雜幾何形狀很容易導致樓梯效應。alketan 等人利用 LPBF 制作了各種周期性金屬胞狀結構,發現由于表面胞狀結構的傾斜角不斷變化,因此與基于支柱的品格相比,表面胞狀結構中的階梯效應不那么明顯,如圖(a, b)所示。
影響 AMed 零件表面粗糙度的第二個因素是部分熔化的粉末當在 AM 過程中使用低能量輸入時,粉末可以部分熔化并粘附在零件表面。由于部分熔化而產生的平均表面粗糙度可以達到與粒度相同的尺度。此外,與較小的粉末相比,較大尺寸的粉末更難完全熔化,從而導致較差的表面光潔度。不同的表面取向也導致了不同的表面粗糙度。在我們之前的工作中,我們報道了由于有更多的部分熔化的粉末,側表面比頂表面具有更高的表面粗糙度,如圖(c, d)所示。此外,眾所周知,由于更多的粉末傾向于部分熔化并粘附在下表面,因此下表面通常比上表面具有更大的表面粗糙度。
在 AM 過程中,起球效應是一個相當普遍的問題,甚至被認為是金屬 AM
中表面缺陷和氣孔的主要原因之一,尤其是鋁合金等輕質合金。它發生在 AM
過程中,因為液態金屬的表面張力通過產生液體球體使表面積最小化。成球效應是一種復雜的冶金行為,它是由潤濕性差和液滴飛濺引起的。如果能量輸入不足,則熔池下部太淺,無法充分滲透到下部層,它不能克服上部的表面張力。這種較差的潤濕性,直接導致液球的形成。
液球的形成。例如,在圖 (e)中,隨著激光掃描速度的增加(能量輸入的減少),熔池被拉長。伴隨著潤濕性的降低,它往往會破裂成不連續的小球。在一定程度上增加能量輸入,可以改善潤濕性,抑制成球效應。然而,過多的能量輸入可能會因液滴飛濺而再次誘發成球效應,如圖 (f)所示。如此高的能量密度會產生不穩定的熔池,伴隨著金屬的蒸發和較大的反沖壓力,致熔化的金屬和未熔化的粉末飛濺。濺落的液態金屬形成微尺度的凝固球體落在表面上。由于液體的低粘度和長壽命,這種液滴飛濺誘導的球化效應在高激光功率和低掃描速度的條件下普遍存在。而且,球化效應不僅會導致表面粗糙度增加,還會導致金屬粉末沉積不均勻,并可能誘發孔隙和分層。
最后但并非最不重要的是,表面裂紋也是一個需要關注的關鍵缺陷。Tang 等在 SLM 制造 CM247LC 時采用邊界掃描策略,旨在提高表面光潔度。雖然使用邊界掃描策略獲得了光滑的表面但結果表明,與體塊區域相比,邊界區域存在更多的裂紋,如圖(g)所示。隨后,作者檢查了邊界區和體區晶體結構,分別以粗柱狀晶粒和細長織構晶粒為特征,如圖 (h)所示。表面裂紋沿邊界區域的高角度晶界出現。邊界區較大的柱狀晶粒與高密度的幾何必要位錯(GND)有關,這意味著更高的內應力,從而更高的裂紋敏感性。因此,在表面光潔度和表面附近區域的裂紋之間的權衡是裂紋敏感合金(如鎳基高溫合金)的 AM 的關鍵問題。需要同時考慮這些因素對工藝參數進行仔細優化。
基于粉末的增材制造金屬和合金中多尺度缺陷的類型包括尺寸缺陷、表面質量缺陷、顯微組織缺陷以及成分缺陷。香港理工大學、西北工業大學和香港中文大學的傅銘旺教授等人提出了基于粉末的增材制造金屬和合金過程中的多尺度缺陷,并闡明了各類缺陷形成的潛在機制以及控制方法;總結了金屬增材制造各類缺陷的破壞性和非破壞性檢測方法;介紹了多尺度增材制造缺陷建模的研究進展;分析討論了各類缺陷對增材制造件的拉伸及疲勞力學性能的影響機制。
多尺度缺陷的分類概覽
金屬 AM 部件的性能在很大程度上取 決于其表面質量和微觀結構特征。影響表面質量和微結構的主要因素包括材料性能、設計相關因素、工藝參數和系統設置。不適當的工藝配置可能會在最終的 AMed 組件中引入缺陷,例如孔隙和裂紋。基于現有的金屬 AM 文獻,在 AMed 金屬零件和結構中識別出從毫米到納米尺度的多尺度缺陷。如圖所示,將多尺度缺陷主要分為三大類,即幾何相關缺陷、表面完整性相關缺陷和微結構缺陷。特別地,我們首先將織構柱狀晶粒,復合-結構缺陷和位錯細胞在 AMed 件中普遍存在,并對 AMed 元件的性能產生重要影響。
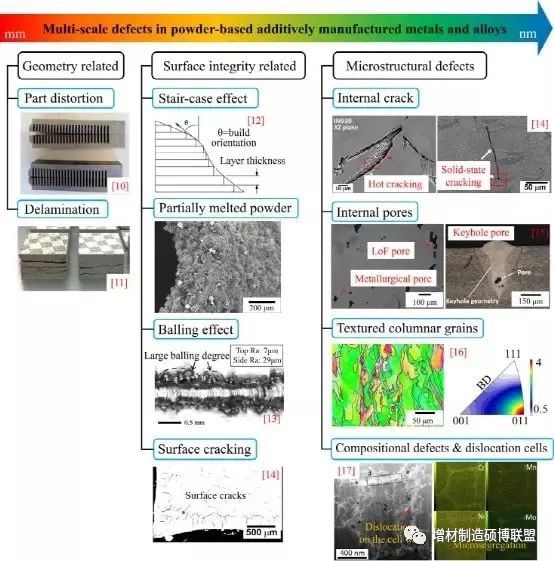
基于粉末的增材制造金屬和合金中多尺度缺陷的分類
1幾何相關缺陷
幾何缺陷主要來自于制造結構與理想 CAD 模型之間 的尺寸和幾何偏差。幾何相關缺陷主要包括零件變形和分層。分層是AM 過程中獨特的開裂行為,這是由于 AM 的逐層制造模式的性質所決定的。典型的零件變形和分層如圖 (a-c)]所示。零件變形和脫層是由宏觀殘余應力引起的,而宏觀殘余應力來源于空間熱 梯度
例如,零件在熱循環過程中的不均勻膨脹和收縮,以及不均勻的非彈性應變。影響殘余應力相關變形的因素有很多。與設備相關的因素包括激光光斑尺寸、基板的厚度和預熱等,都可能誘發這類缺陷。在我們寶貴的工作中,我們比較了微 LPBF(使用直徑為 25 m 的細激光束)和常規 LPBF 產生的懸臂梁的畸變。如圖 (a.d)所示,由于原位應力消除退火更顯著,精細激光束產生的畸變更小。因此,微型 LPBF 系統更有可能生產出幾何精度高的部件。此外,Corbin 等研究了襯底厚度和預熱對 DED Ti6A14V 變形的影響。他們得出結論:襯底預熱后,薄襯底的畸變有效降低,而厚襯底的畸變則增加。因此,選擇合適的基板厚度和預熱溫度來減少殘余應力是很重要的。
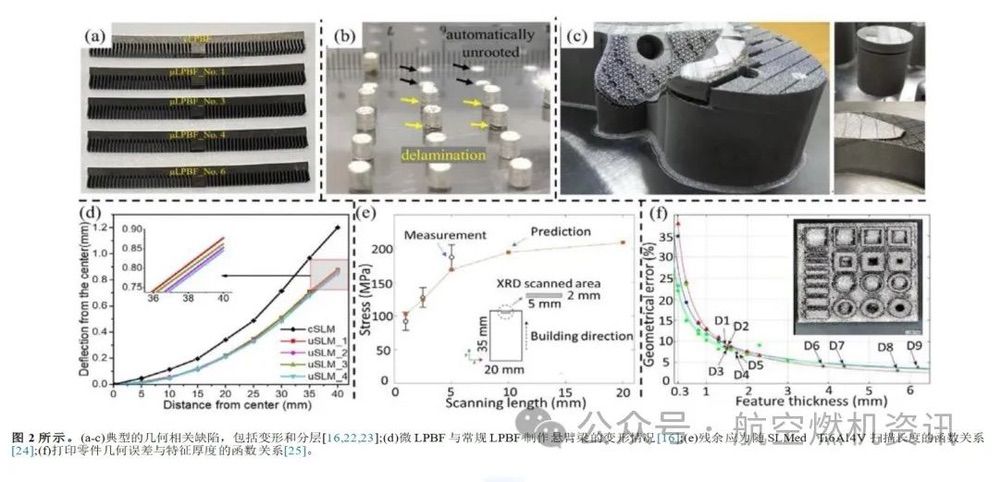
零件變形的設計相關因素包 括零件在基材上的方向和位置、零件形狀、特征尺寸直接金屬激光燒結 Ti6A14V 零件的幾何精度。結果表明,幾何誤差隨著特征尺寸的增加而減小并收斂到一個恒定值,表明尺寸相關收縮是幾何不精度的原因。此外,懸空或突出特征在復雜結構中很常見,但由于缺乏底部支撐,它們難以通過 AM對于 PBF 工藝,粉末床可以作為這些結構的支撐。然而,由于粉末床與固體懸垂結構之間的電導率差異,可能會產生集中的殘余應力,導致結構翹曲、卷曲和變形。因此,當構件具有懸垂或突出特征時,需要設計支撐結構。除了支撐懸垂特征外,良好的支撐結構設計還可以保證正確的熱流流向基材,防止因高殘余應力而產生較大的變形。
2表面完整性相關缺陷
表面完整性缺陷是指與 CAD 設計模型的理想輪廓相偏離的不均勻或不規則的表面特征。我們總結了造成 AMed 部件表面完整性相關缺陷的四個主要因素,即階梯效應、部分熔化的粉末、球化效應和表面裂紋。與機械加工等傳統制造工藝相比,這些缺陷導致表面粗糙度較高,質量和精度較低,這是 AM 工藝固有的局限性之一.
階梯效應是指由于制造分辨率的限制,曲面和斜面的層層逐級通近。樓梯效應引起的平均表面粗糙度(Ra)由層厚度和相對于建筑方向的傾斜角(BD)決定。增加層厚會導致顯著的樓梯效應和更大的表面粗糙度。對于 AM 的晶格結構,這種帶有懸挑支柱的復雜幾何形狀很容易導致樓梯效應。alketan 等人利用 LPBF 制作了各種周期性金屬胞狀結構,發現由于表面胞狀結構的傾斜角不斷變化,因此與基于支柱的品格相比,表面胞狀結構中的階梯效應不那么明顯,如圖(a, b)所示。
影響 AMed 零件表面粗糙度的第二個因素是部分熔化的粉末當在 AM 過程中使用低能量輸入時,粉末可以部分熔化并粘附在零件表面。由于部分熔化而產生的平均表面粗糙度可以達到與粒度相同的尺度。此外,與較小的粉末相比,較大尺寸的粉末更難完全熔化,從而導致較差的表面光潔度。不同的表面取向也導致了不同的表面粗糙度。在我們之前的工作中,我們報道了由于有更多的部分熔化的粉末,側表面比頂表面具有更高的表面粗糙度,如圖(c, d)所示。此外,眾所周知,由于更多的粉末傾向于部分熔化并粘附在下表面,因此下表面通常比上表面具有更大的表面粗糙度。

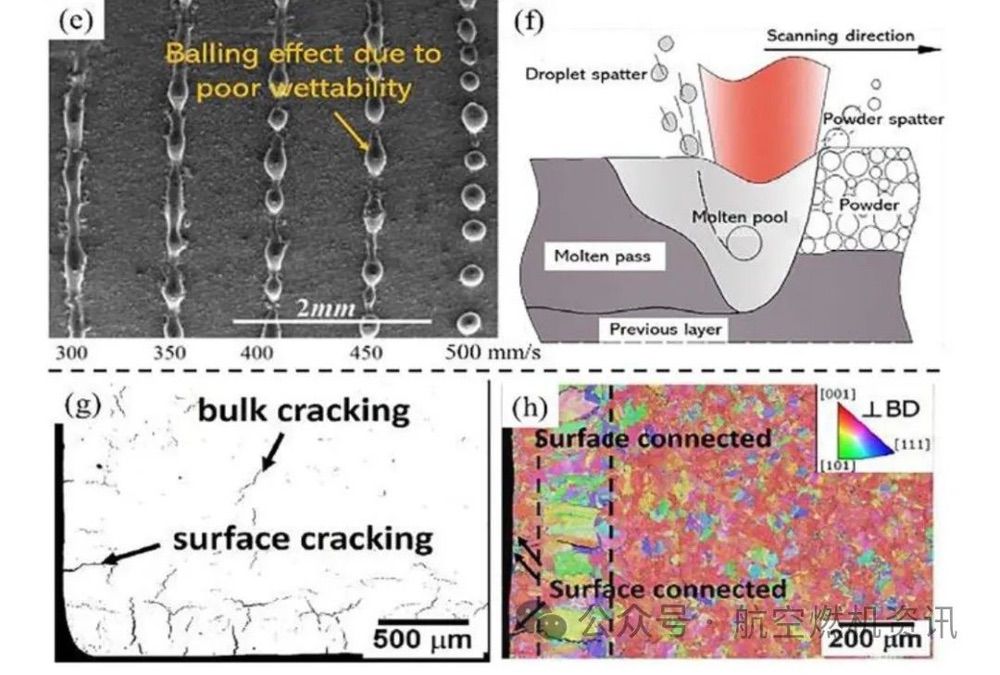
液球的形成。例如,在圖 (e)中,隨著激光掃描速度的增加(能量輸入的減少),熔池被拉長。伴隨著潤濕性的降低,它往往會破裂成不連續的小球。在一定程度上增加能量輸入,可以改善潤濕性,抑制成球效應。然而,過多的能量輸入可能會因液滴飛濺而再次誘發成球效應,如圖 (f)所示。如此高的能量密度會產生不穩定的熔池,伴隨著金屬的蒸發和較大的反沖壓力,致熔化的金屬和未熔化的粉末飛濺。濺落的液態金屬形成微尺度的凝固球體落在表面上。由于液體的低粘度和長壽命,這種液滴飛濺誘導的球化效應在高激光功率和低掃描速度的條件下普遍存在。而且,球化效應不僅會導致表面粗糙度增加,還會導致金屬粉末沉積不均勻,并可能誘發孔隙和分層。
最后但并非最不重要的是,表面裂紋也是一個需要關注的關鍵缺陷。Tang 等在 SLM 制造 CM247LC 時采用邊界掃描策略,旨在提高表面光潔度。雖然使用邊界掃描策略獲得了光滑的表面但結果表明,與體塊區域相比,邊界區域存在更多的裂紋,如圖(g)所示。隨后,作者檢查了邊界區和體區晶體結構,分別以粗柱狀晶粒和細長織構晶粒為特征,如圖 (h)所示。表面裂紋沿邊界區域的高角度晶界出現。邊界區較大的柱狀晶粒與高密度的幾何必要位錯(GND)有關,這意味著更高的內應力,從而更高的裂紋敏感性。因此,在表面光潔度和表面附近區域的裂紋之間的權衡是裂紋敏感合金(如鎳基高溫合金)的 AM 的關鍵問題。需要同時考慮這些因素對工藝參數進行仔細優化。
(責任編輯:admin)
最新內容
熱點內容