大型零件多機器人協同電弧增材制造層內沉積路徑的分配與調度
時間:2024-01-18 09:20 來源:WAAM電弧增材 作者:admin 閱讀:次
增材制造(AM)目前應用廣泛,其中大型金屬零件的增材制造已被確定為一個有前景的研究方向。電弧增材制造(WAAM)由于具有成本低和效率高的優點,更適合用于制造具有大尺寸幾何形狀和結構較為復雜的零件。此外,WAAM可以很容易地集成到工業機器人中,這有利于提高制造的自由度,并減小了制造零件的尺寸限制。
然而,通過單個增材制造系統,制造米尺度下的零件仍然需要數周甚至更長時間。長期沉積工藝需要高水平的系統穩定性,以確保生產零件無缺陷。為了提高制造效率,多機器人協作WAAM(MRC-)已經被推廣,這需要多個機器人AM系統協同工作。
在此基礎上,東南大學李永哲副教授及其團隊在知名期刊 Virtual and Physical Prototyping(IF=10.6)上發表題目為 “Allocation and scheduling of deposition paths in a layer for multi-robot coordinated wire and arc additive manufacturing of large-scale parts”的研究論文。基本步驟是在執行實際沉積工藝之前,為每層分配和調度機器人沉積路徑。為機器人分配沉積路徑并且在考慮最短總工作時間、工作量和安全的情況下調度沉積過程。其難點來自算法的高時間復雜度。在這些難點的驅動下,此研究提到的方法旨在開發一種算法解決方案,以促進MRC-WAAM過程規劃。
研究目的
本研究旨在解決多機器人協同電弧增材制造(MRC-WAAM)系統中的關鍵問題:如何有效地分配和調度每層的沉積路徑。這一挑戰源于優化機器人工作時間、任務量和沉積順序時面臨的高時間復雜性。研究團隊創新開發了一種的“top k%”方法,通過迭代方式將k%長度的路徑從任務庫分配給當前工作任務量最少的機器人,直到所有路徑被分配完畢。這一方法能夠使各機器人的任務量均等,同時提高分配結果中路徑的相鄰性,從而提高MRC-WAAM的成形質量。
研究方法
本研究提出的“top k%”方法在數學上通過一個執行成本矩陣來定義。該方法通過計算工作時間和路徑距離來分配任務,并以最小化所有機器人的總工作時間為目標。研究中還考慮了路徑的鄰接性和機器人間的安全距離,以確保沉積過程中不會發生機器人之間的碰撞。
為了驗證算法的有效性,研究團隊構建了一個包含三個YASKAWA AR1730工業6軸機器人和MEGMEET Artsen Plus 500Q焊接電源的測試平臺。使用了特定的材料和參數,通過MATLAB R2021b實現了分配和調度算法。實驗分為兩個階段:一是在四個不同長度和路徑數量的大型零件模型上驗證算法的可行性,二是選取一個模型進行實際的沉積驗證。結果表明,該方法在減少轉折點次數和起弧點方面優于現有解決方案,驗證了其在實際應用中的有效性。
論文圖片
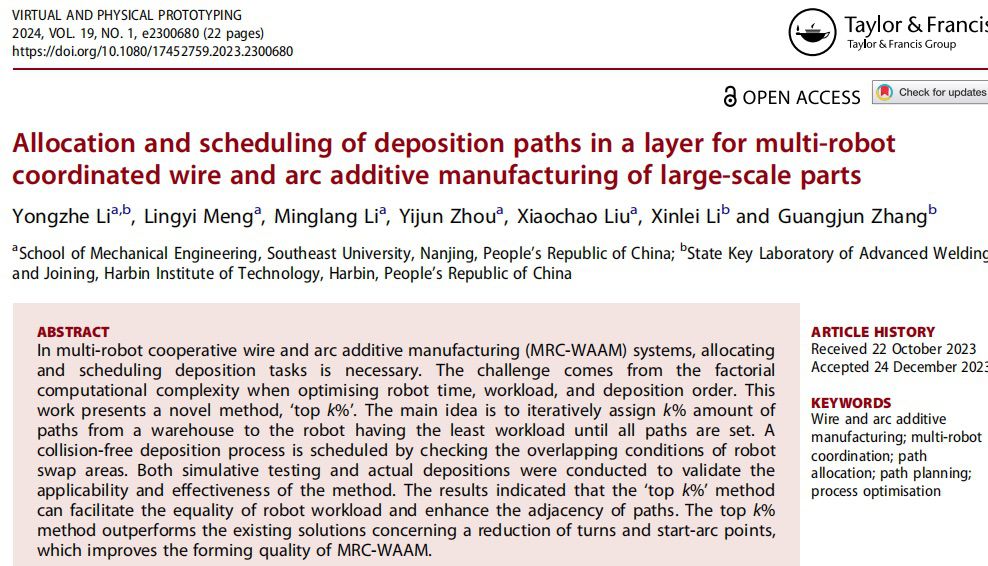
然而,通過單個增材制造系統,制造米尺度下的零件仍然需要數周甚至更長時間。長期沉積工藝需要高水平的系統穩定性,以確保生產零件無缺陷。為了提高制造效率,多機器人協作WAAM(MRC-)已經被推廣,這需要多個機器人AM系統協同工作。
在此基礎上,東南大學李永哲副教授及其團隊在知名期刊 Virtual and Physical Prototyping(IF=10.6)上發表題目為 “Allocation and scheduling of deposition paths in a layer for multi-robot coordinated wire and arc additive manufacturing of large-scale parts”的研究論文。基本步驟是在執行實際沉積工藝之前,為每層分配和調度機器人沉積路徑。為機器人分配沉積路徑并且在考慮最短總工作時間、工作量和安全的情況下調度沉積過程。其難點來自算法的高時間復雜度。在這些難點的驅動下,此研究提到的方法旨在開發一種算法解決方案,以促進MRC-WAAM過程規劃。
研究目的
本研究旨在解決多機器人協同電弧增材制造(MRC-WAAM)系統中的關鍵問題:如何有效地分配和調度每層的沉積路徑。這一挑戰源于優化機器人工作時間、任務量和沉積順序時面臨的高時間復雜性。研究團隊創新開發了一種的“top k%”方法,通過迭代方式將k%長度的路徑從任務庫分配給當前工作任務量最少的機器人,直到所有路徑被分配完畢。這一方法能夠使各機器人的任務量均等,同時提高分配結果中路徑的相鄰性,從而提高MRC-WAAM的成形質量。
研究方法
本研究提出的“top k%”方法在數學上通過一個執行成本矩陣來定義。該方法通過計算工作時間和路徑距離來分配任務,并以最小化所有機器人的總工作時間為目標。研究中還考慮了路徑的鄰接性和機器人間的安全距離,以確保沉積過程中不會發生機器人之間的碰撞。
為了驗證算法的有效性,研究團隊構建了一個包含三個YASKAWA AR1730工業6軸機器人和MEGMEET Artsen Plus 500Q焊接電源的測試平臺。使用了特定的材料和參數,通過MATLAB R2021b實現了分配和調度算法。實驗分為兩個階段:一是在四個不同長度和路徑數量的大型零件模型上驗證算法的可行性,二是選取一個模型進行實際的沉積驗證。結果表明,該方法在減少轉折點次數和起弧點方面優于現有解決方案,驗證了其在實際應用中的有效性。
論文圖片

圖1.直接將切片分割成子區域來進行MRC-AM的路徑規劃示意

圖2.為MRC-WAAM分配沉積路徑的總體工作流程

圖3.使用“top k%”方法進行多機器人沉積路徑分配算法流程
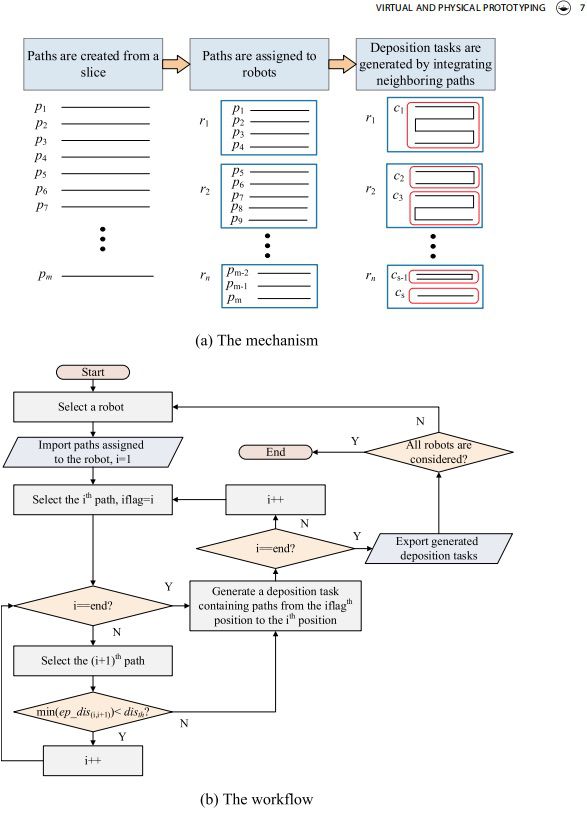
圖4. 沉積任務生成算法流程
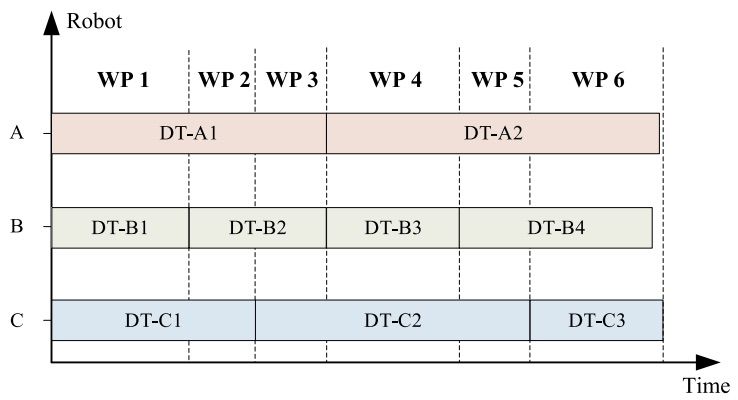
圖5.定義沉積計劃的工作階段(WPs)
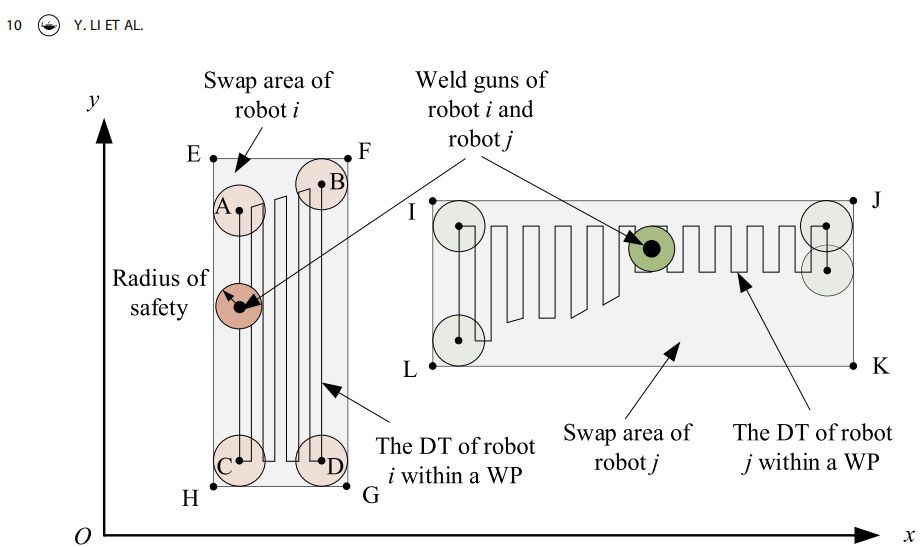
圖6.檢查WP內機器人掃過區域是否發生干涉
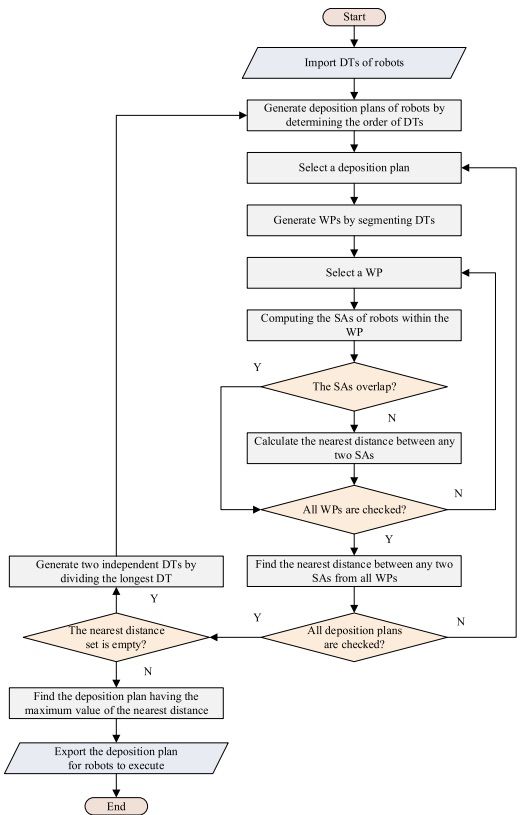
圖7. MRC-WAAM系統調度生成沉積任務順序的算法流程
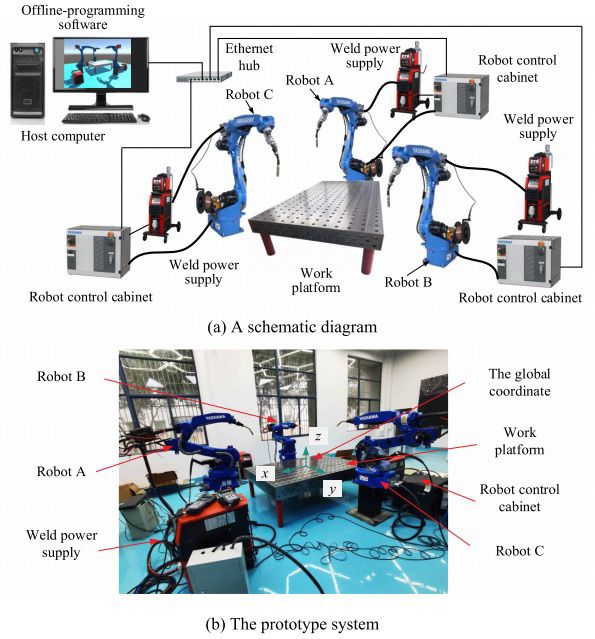
圖8. 實驗驗證平臺

圖9.機器人與零件中心之間的空間位置關系
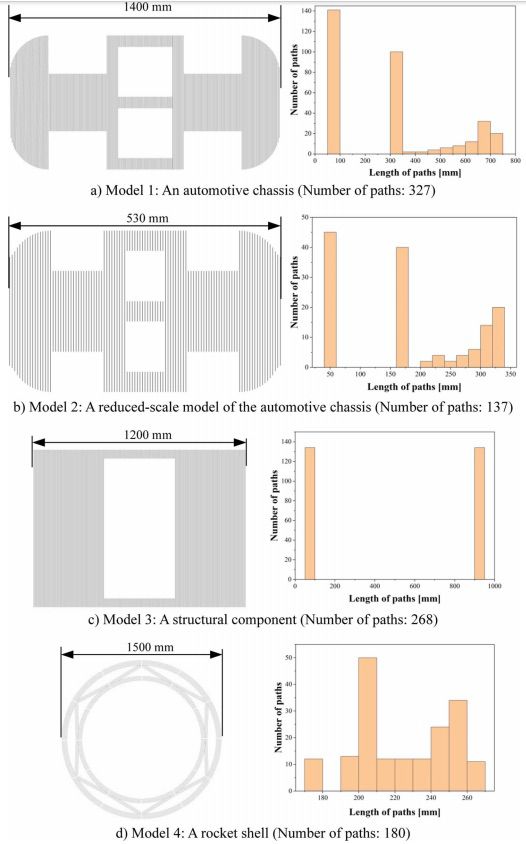
圖10.用于驗證的增材制造切片模型
(責任編輯:admin)
最新內容
熱點內容