中國團隊顛覆3D打印極限!室溫 865MPa、耐 400℃ 鋁合金誕生
中國科學家突破 3D 打印鋁合金極限,打造超高強度耐熱新材料!近日,中國科學院金屬研究所團隊在《材料科學與技術》期刊發表重磅研究成果,宣布通過激光粉末床融合( LPBF ,即金屬 3D 打印)技術成功制備出一種名為 Al-Fe-V-Si-Sc 的新型鋁合金。該材料不僅室溫下抗拉強度高達 865 兆帕,更在 400 ℃高溫下仍保持優異性能,填補了傳統鋁合金在 200-450 ℃溫區的技術空白,為航空航天及汽車工業輕量化發展提供了全新解決方案。
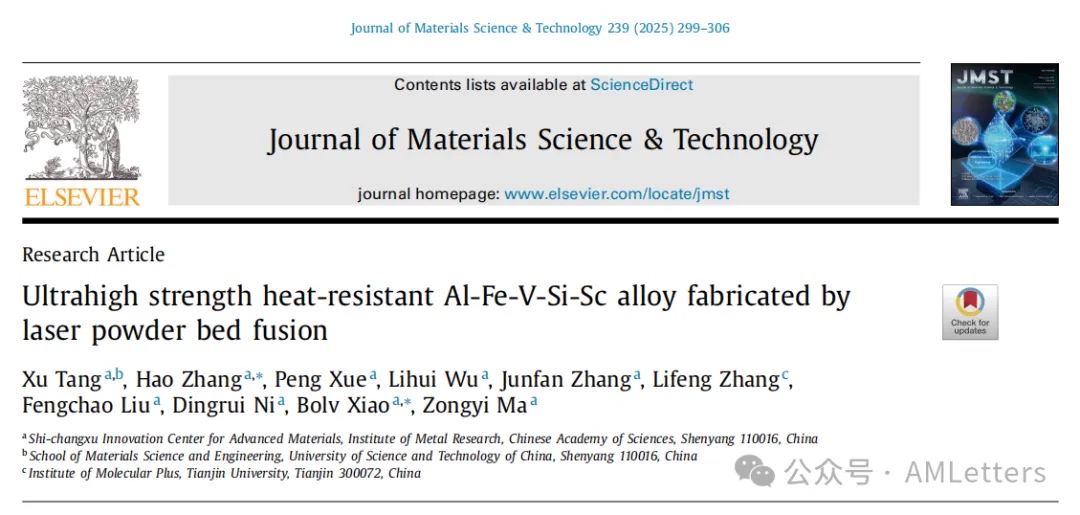
技術突破:微合金設計與激光打印協同發力
研究團隊創新性地在 Al-Fe-V-Si 合金中添加微量鈧( Sc )元素,并利用 LPBF 技術超高速冷卻(達 10⁷ K/s )的特性,成功抑制了材料在打印過程中常見的熱裂紋缺陷。通過優化激光功率、掃描速度等參數,團隊實現了 99.9% 的致密度,攻克了高強鋁合金 3D 打印易開裂的行業難題。微觀結構分析顯示,材料內部形成了獨特的 “非晶 / 晶體復合結構”:熔池中心因極速冷卻形成非晶態帶狀網絡,邊界則分布著 Al8Fe2Si、Al10V 等多種納米級析出相。
鈧元素的加入進一步促使 Al3Sc 界面相生成,有效阻止高溫下納米顆粒的粗化,使材料兼具超高強度和熱穩定性。
性能卓越:室溫至高溫全面領先
實驗數據顯示,該合金室溫下抗拉強度高達 865 兆帕、硬度達 360 HV ,抗拉強度較現有 3D 打印鋁合金提升約 30% ,且高溫性能表現尤為突出—— 400 ℃時仍保有 450 兆帕的抗拉強度,遠超傳統鋁合金及部分鈦合金。這種多尺度相協同強化的設計思路,為未來高性能增材制造材料開發提供了新范式。
應用前景:復雜構件一體化成型
研究還展示了該合金在復雜格柵結構零件制造中的潛力。由于 LPBF 技術可實現材料-結構-性能一體化成型,該合金有望直接用于發動機耐熱部件、航天器輕量化支架等關鍵領域,大幅降低加工成本并提升設計自由度。
目前,正進一步探索該合金的規模化制備工藝及長期熱穩定性驗證。此項突破不僅推動了鋁合金在極端環境下的應用邊界,更為我國高端裝備制造提供了自主可控的材料技術儲備。
主要附圖
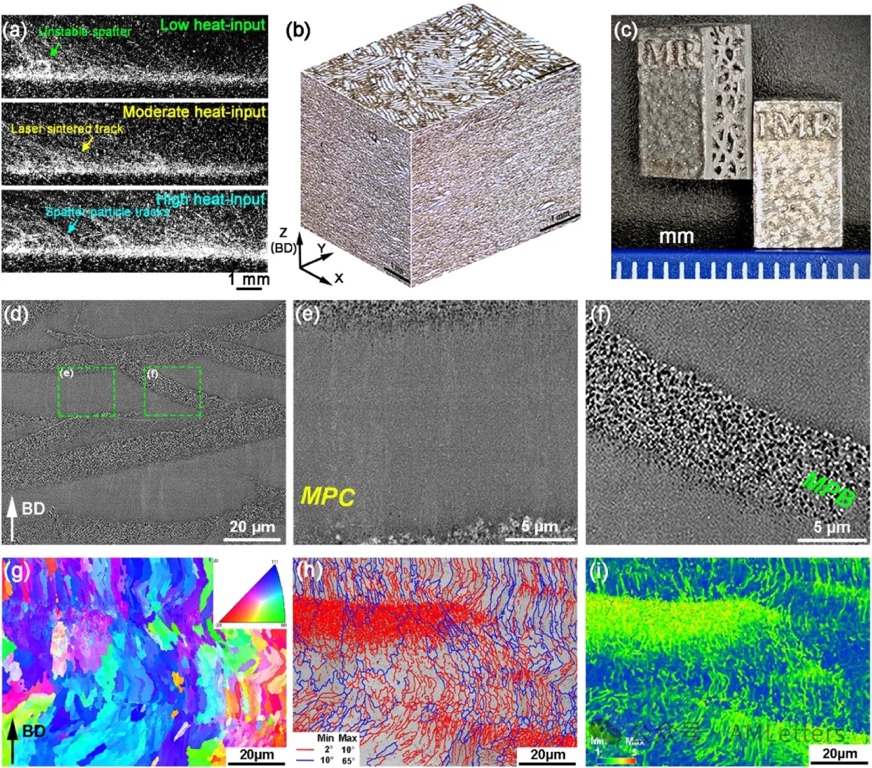
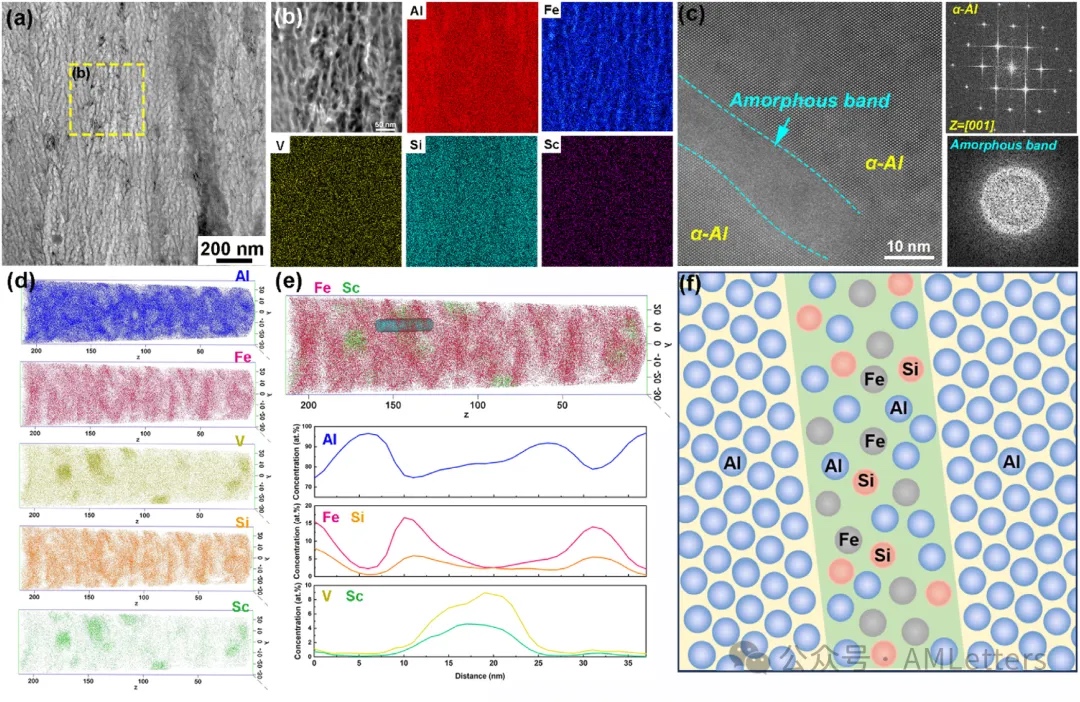
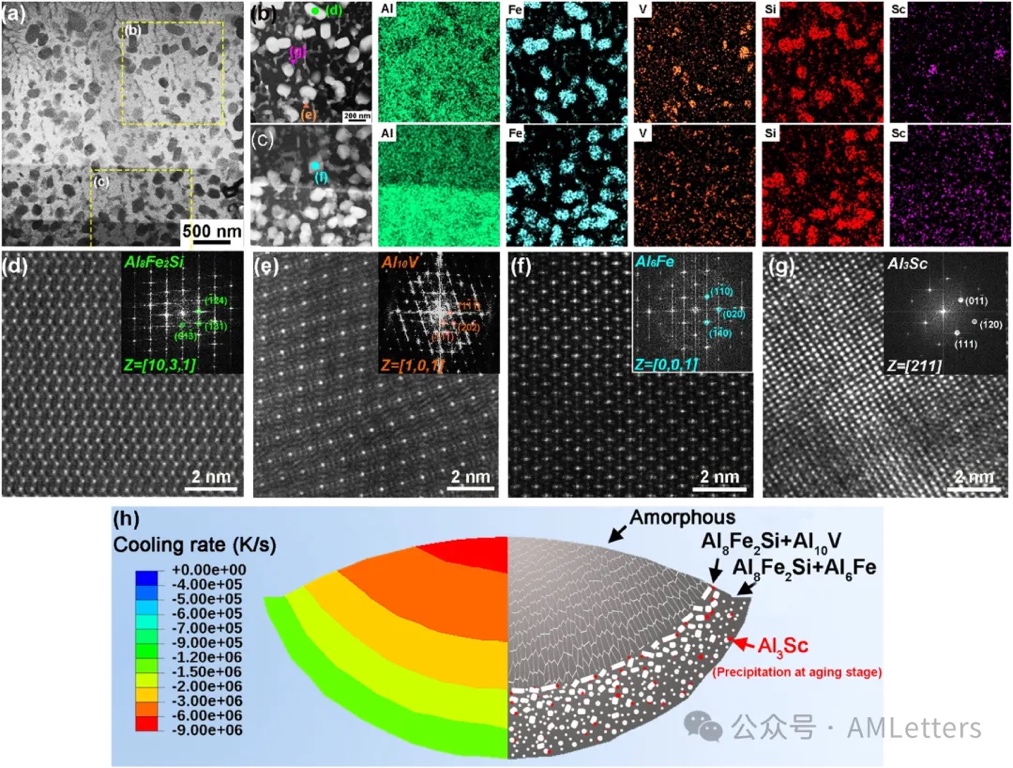
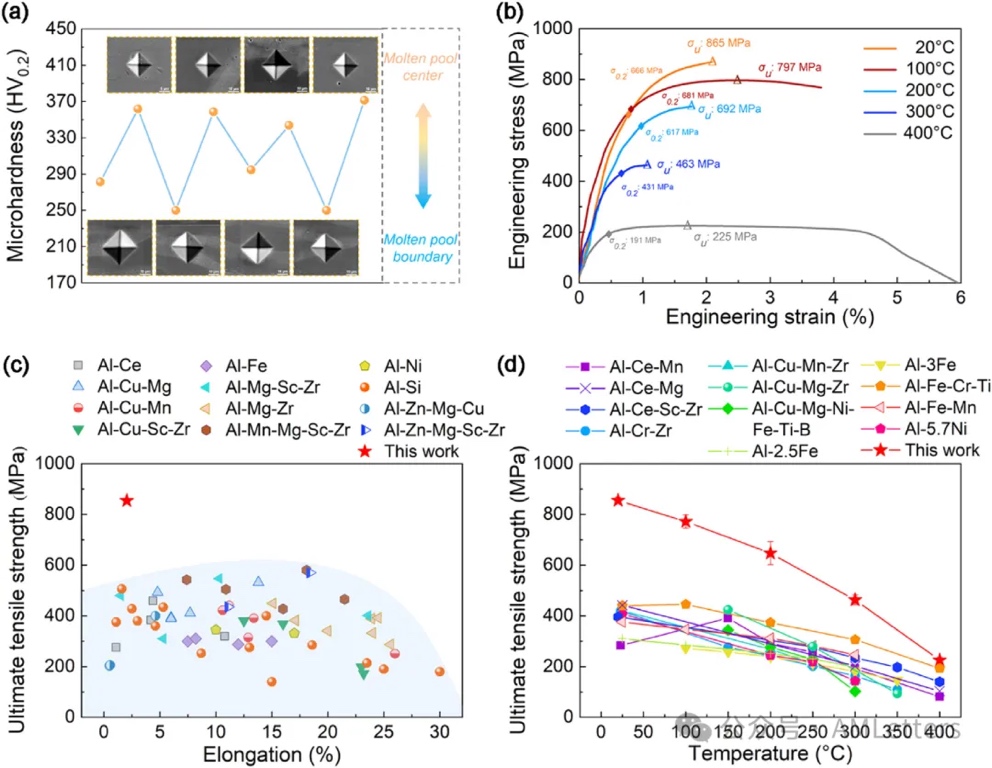
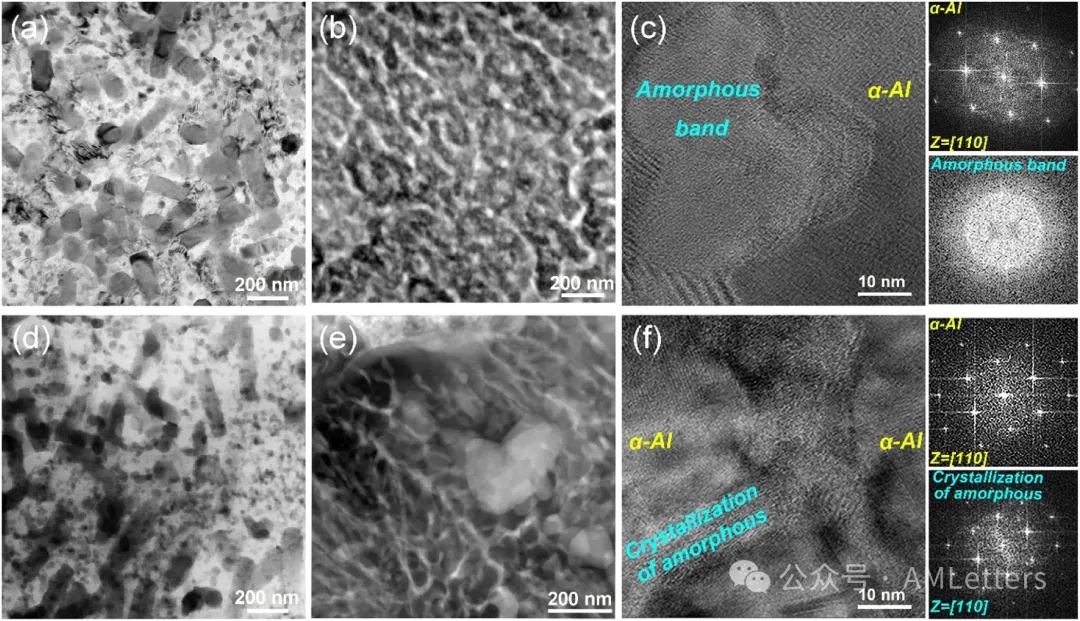
AMLetters 點評
1. 三項關鍵技術突破:
非晶 / 晶體復合結構: 激光粉末床融合( LPBF )的極速冷卻( 10 ⁷ K/s )使熔池中心形成非晶態網絡,通過阻礙位錯運動提升強度。
多尺度析出相協同強化: 熔池邊界分布的Al₈Fe₂Si、Al₁₀V等納米析出相(10-100 nm)通過奧羅萬機制強化基體,而Al₃Sc 界面相抑制高溫下顆粒粗化。
鈧元素的晶界調控: Sc 元素細化晶粒并釘扎晶界,顯著降低熱裂紋敏感性。
啟示: 3D 打印的非平衡加工特性成為解鎖材料性能的關鍵,而非傳統認知中的“工藝缺陷”。
2. 工程化應用的潛在挑戰
盡管實驗室數據亮眼,大規模應用仍需解決以下問題:
成本瓶頸: 鈧( Sc )作為稀有金屬,價格高昂(約 1.5 萬元 / 公斤),亟需開發低成本替代方案或回收技術。
工藝穩定性: 實驗室級參數(如激光功率 275 W 、掃描速度 1600 mm/s )在量產中易受粉末流動性、設備波動影響,致密度可能下降。
長期熱穩定性: 400 ℃下短期強度優異,但航空發動機等場景需驗證 5000 小時以上的高溫耐久性,目前數據尚未覆蓋。
思考:這與高溫合金、碳纖維等材料的產業化路徑相似 ——從實驗室到工程化,往往需要跨越“最后一公里”的技術鴻溝。
3. 技術顛覆性與行業影響
設計自由度提升: LPBF 允許在零件內部定向調控非晶 / 納米相分布,未來或實現“應力集中區強化 + 輕量化區域減薄”的一體化設計。
替代鈦合金的潛力: 若該合金替代航空鈦合金部件,可減重 20%-30% ,僅燃油效率提升一項,單架客機年省成本超百萬美元。
國產化意義: 我國 部分高端材料 長期依賴進口, 近年來借助國內增材制造技術的快速發展,部分領域有彎道超車之勢,該材料就是一個典型案例, 此項技術突破為航天、核電等領域提供了自主可控的新選項。
(責任編輯:admin)