激光粉末床聚變增材制造過程的原位時間分辨X射線成像和衍射儀(2)
時間:2023-01-19 20:07 來源:激光粉末床聚變增材制造 作者:admin 閱讀:次
比較了兩種系統:一種是基材支撐在兩個玻璃碳窗口之間的情況,如本文所述的實驗,另一種是兩個窗口由Ti-64組成,以模擬大塊LPBF情況。這兩種情況都使用ε=0.6的輻射邊界條件。模型的幾何結構如圖4(a)所示。激光光斑的測量強度如圖4(b)所示。
元素Ti的溫度相關蒸汽壓和蒸發熱值被用作Ti-64合金值的近似值。它忽略了熔池中的Marangoni流動,因此無法準確計算熔池內的熱梯度,但這不會影響遠離熔池的固體冷卻的準確性。圖4(c)顯示了激光位置處Ti-64襯底內的二維熱分布。兩種情況下的比較熱分布見圖4(d)和4(e)。兩種情況下的熱分布之間的差異小得可以忽略不計,因此我們得出結論,對于裸板情況,玻碳窗的熱邊界條件基本上不會影響這些條件下的熔池動力學。通過金屬板的熱傳導比通過粉末層的傳導至少大1個數量級;因此在粉末情況下,通過板的傳導也應占主導地位。使用衍射對冷卻期間的晶格動力學進行的任何分析都必須包括徹底的建模,以了解熱邊界條件對測量衍射圖案的影響。

圖4熱邊界條件對薄襯底中熱傳輸的影響。
粉末床熔融(PBF)包括利用激光或電子束能量源的過程。這兩種技術在操作上本質上是相似的,在平臺降低并重復循環之前,在構建平臺上反復鋪上一層松散的粉末,然后將其熔化并與前一層融合。不同的能源需要不同的操作環境。對于激光系統,需要惰性氣氛,通常是氮氣或氬氣。電子束過程需要近真空,因為電子的平均自由程非常短,另一個好處是沒有氧氣引起氧化。在熔化過程中,氦氣分壓在大約 10×10-2mbar 并針對構建區域,以增強組件的傳熱和冷卻。
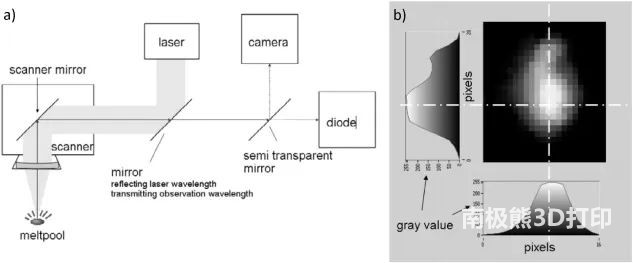
(a)顯示光電二極管和相機排列的示意圖,以及(b)顯示Berumen等人實現的不同強度值的相機系統輸出的示例(右)。
X射線成像
在SSRL射束線2-2上進行了X射線成像實驗。該射束線上可用的X射線由臨界能量為7.4keV的1.25 T彎曲磁體產生。圖5(a)顯示了該彎曲磁體產生的計算X射線光譜。將6.35mm厚的鋁板用作樣品上游的X射線過濾器,以去除低能X射線,并保護檢測系統免受彎曲磁體源的完全發射的損壞。使用該過濾的X射線光譜進行原位成像實驗,以最大化高能X射線通量。
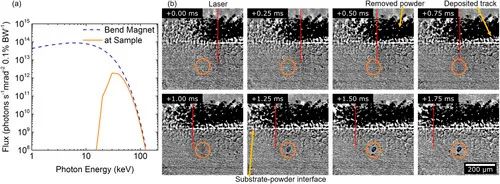
圖5是典型熔池區域的X射線成像。
使用高速成像裝置記錄通過樣品和室的X射線。透射的X射線首先擊中了直接位于腔室出口Be窗口后面的摻Tl的NaI閃爍體晶體,該晶體將X射線光子轉換為可見光。
蒸汽凹陷深度和形狀很難用表面敏感光學技術測量,但由于蒸汽凹陷中存在的固體/液體Ti-64和Ar氣體之間的顯著密度對比。此外,垂直于激光束及其路徑的2D投影的透視圖對于測量凹陷深度和形狀非常有用。因此,這些測量值對于模型驗證具有很高的價值。
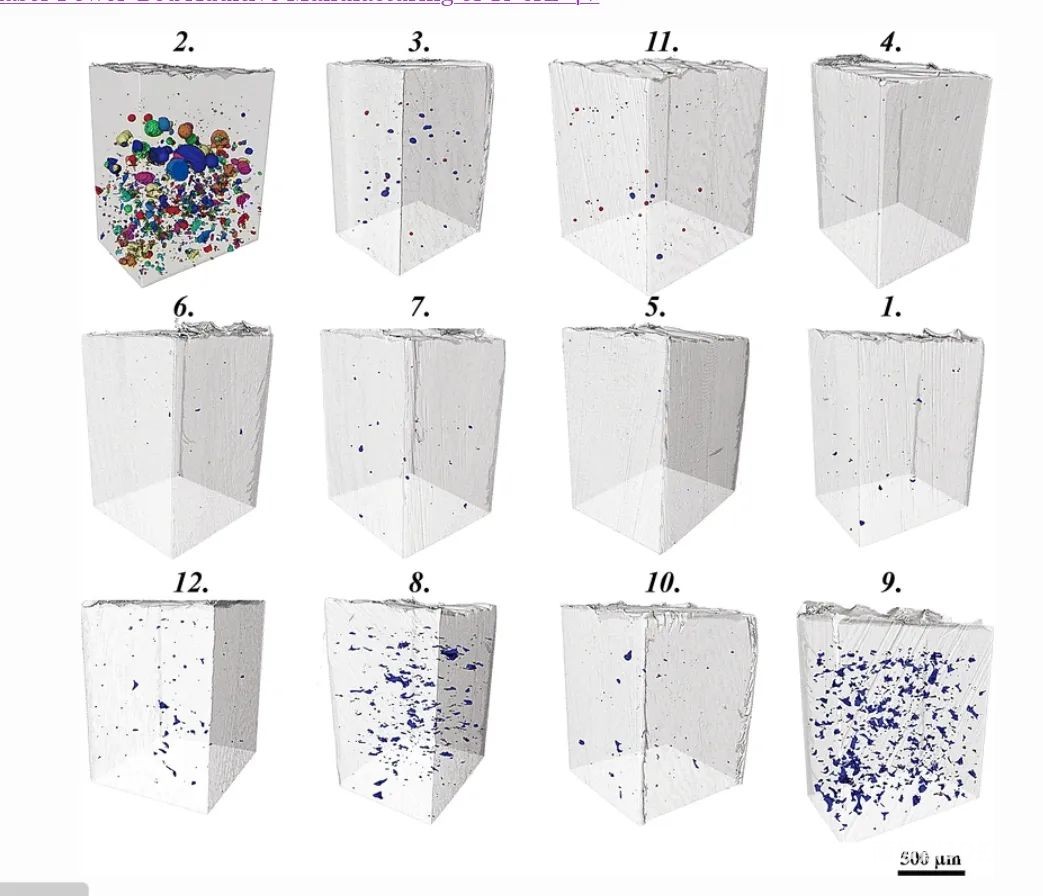
按重疊深度遞減順序預測樣品的μSXCT重建。
上圖給出了每個樣品頂部1.5 mm的三維(3D)斷層掃描重建的投影,按熔池重疊深度排序。應該注意的是,在 3D 投影中查看孔隙率會夸大樣品內孔隙的體積分數。孔隙按形態分割和著色。由于其缺陷種群明顯較大,因此由單個孔隙著色。雖然形態不是確定缺陷形成機制的決定性指標,但可以合理地假設高度球形的孔很可能是由凝固過程中捕獲的不溶性氣泡形成的,而大部分不規則的孔很可能缺乏熔合缺陷。在本實驗中,各向異性值0.5用作“球形”孔的最大截止值。
X射線衍射
圖6顯示了從500μm厚的Ti-64襯底上采集的典型衍射數據~60μm厚粉末層。以1kHz的采樣率收集數據,并將激光設置為400W的功率,掃描速度為576mm/s。X射線束與束中心對齊,如圖6(a)所示,基板頂部以下25μm。在這種幾何結構中,整個采樣體積在基底內,粉末層的貢獻最小。圖6(b)顯示了在1kHz下收集的1500個衍射圖案的總和,相當于1.5秒的收集。圖6(c)顯示了激光熔化前在1kHz下收集的二維衍射圖案。圖6(d)顯示了在1kHz下收集的積分一維衍射圖案的時間序列。激光熔化前后收集的衍射圖顯示了三個α-Ti峰的峰形狀和位置的差異,表明宏觀和微觀應變狀態發生了變化。這些對冷卻過程中快速晶體變化的觀察,為LPBF制造材料的獨特微觀結構特征提供了見解。
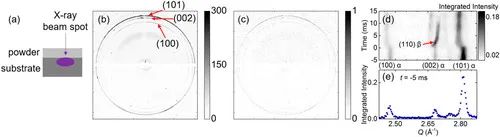
圖6 在SSRL光束線10-2處收集的衍射圖案。
結論
我們報告了實驗室規模的LPBF儀器的設計和實施,該儀器經過優化,可在同步輻射源上進行原位X射線實驗,同時提供代表全尺寸LPBF機器的環境。在SSRL進行的實驗產生了4 kHz成像數據,有效像素大小為1.1μm,并從50 × 100μm區域產生了1 kHz衍射數據。對數據的初步檢查揭示了 Ti-64 中孔隙形成、熔體凹陷動力學、溫度依賴性晶格動力學以及冷卻時的β-Ti–α-Ti 相變。檢測方案和樣品架的持續升級將實現多層實驗,更快的樣品制備以獲得更高的通量,并改善信噪比以提高最大可實現的采樣率。未來的實驗將包括與光學過程監測器的集成,以促進亞表面缺陷形成與表面敏感光學檢測方法之間的相關性。這種相關性將通過LPBF期間的在線過程監控直接洞察缺陷檢測,這對于LPBF零件的鑒定和認證是一項重大挑戰。
來源:An instrument for in situ time-resolved X-ray imaging and diffraction of laser powder bed fusion additive manufacturing processes, Review of Scientific Instruments, doi.org/10.1063/1.5017236
參考文獻:W. E. King, A. T. Anderson, R. M. Ferencz, N. E. Hodge, C. Kamath, S. A. Khairallah, and A. M. Rubenchik, Appl. Phys. Rev. 2, 041304 (2015). https://doi.org/10.1063/1.4937809;R. P. Mulay, J. A. Moore, J. N. Florando, N. R. Barton, and M. Kumar, Mater. Sci. Eng. A 666, 43 (2016). https://doi.org/10.1016/j.msea.2016.04.012
(責任編輯:admin)
最新內容
熱點內容